In the realm of ancient craftsmanship, few creations are as revered and iconic as the Japanese katana sword. This legendary weapon, renowned for its exceptional sharpness, strength, and beauty, has captivated the imagination of warriors and artisans for centuries. Crafting a real katana sword is not merely a technical endeavor; it is a profound journey that blends traditional techniques with the soul of the swordsmith. In this article, we will explore the meticulous process of forging and crafting a genuine katana sword, a pursuit reserved for the most skilled and dedicated artisans.
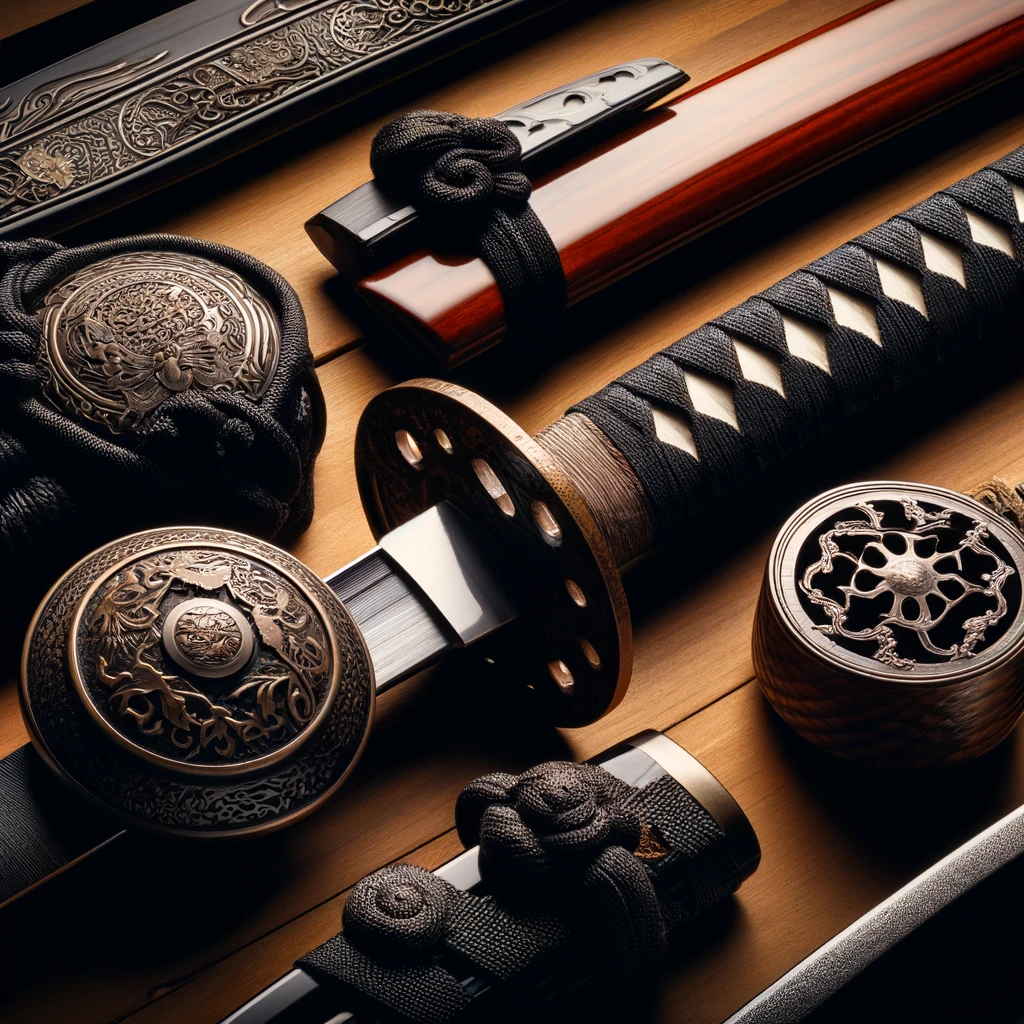
1. The Spirit of the Swordsmith: At the heart of crafting a katana lies the spirit of the swordsmith, whose dedication and reverence for the craft are paramount. Before embarking on the physical creation of the sword, the swordsmith must cultivate a deep understanding of the katana’s history, significance, and spiritual essence. This spiritual connection forms the foundation upon which every step of the crafting process is built.
2. Selecting the Materials: The journey begins with the careful selection of materials, a task that requires precision and discernment. The blade of a katana is typically made from tamahagane, a type of high-carbon steel renowned for its strength and flexibility. This raw material is sourced from iron sand and undergoes a complex smelting process to purify and refine it into steel suitable for forging. The selection of the right materials is crucial, as it determines the quality and performance of the final sword.
3. Forging the Blade: With the materials in hand, the swordsmith begins the intricate process of forging the blade. This stage requires both technical expertise and artistic finesse. The tamahagane steel is heated to extreme temperatures in a traditional charcoal forge and hammered repeatedly to shape and refine it into the iconic curved blade of the katana. Throughout this process, the swordsmith must carefully control the temperature and pressure to ensure the blade’s strength and integrity.
4. Folding and Layering: One of the most distinctive features of a katana blade is its characteristic grain pattern, known as hada. This pattern is achieved through the ancient technique of folding and layering the steel. The swordsmith meticulously folds the steel multiple times, creating hundreds or even thousands of layers that are visible in the finished blade. This process not only enhances the blade’s strength and durability but also adds to its aesthetic appeal.
5. Tempering and Quenching: After forging and shaping the blade, it undergoes the crucial processes of tempering and quenching. Tempering involves heating the blade to a specific temperature and then rapidly cooling it to achieve the desired hardness and resilience. Quenching, on the other hand, involves immersing the hot blade in a quenching medium, such as water or oil, to further harden and strengthen it. These steps are essential for creating a blade that is both sharp and durable.
6. Polishing and Finishing: With the blade forged and tempered, the swordsmith turns his attention to the final stages of polishing and finishing. This meticulous process involves grinding, polishing, and sharpening the blade to perfection, revealing its true beauty and luster. Each stroke of the polishing stone is executed with precision and care, bringing out the intricate details of the hada pattern and creating a mirror-like finish that reflects the craftsmanship of the swordsmith.
7. Crafting the Fittings: In addition to the blade, a katana sword is adorned with a variety of fittings, including the tsuba (handguard), tsuka (handle), and saya (scabbard). These fittings are crafted with the same level of attention to detail and craftsmanship as the blade itself. The tsuba, often elaborately decorated with intricate designs, serves both a functional and decorative purpose, while the tsuka and saya are carefully shaped and finished to complement the overall aesthetic of the sword.
8. Honing the Edge: The final step in crafting a katana sword is honing the edge to razor-sharp perfection. This delicate task requires the utmost skill and precision, as the swordsmith carefully sharpens and refines the blade to achieve the legendary cutting ability for which the katana is renowned. With each stroke of the sharpening stone, the edge of the blade is honed to an unparalleled level of sharpness, ready to slice through any obstacle with ease.
Conclusion: Crafting a real katana sword is not simply an act of creation; it is a labor of love, dedication, and reverence for tradition. From the selection of materials to the final honing of the edge, every step in the process is imbued with the spirit of the swordsmith and the centuries of craftsmanship that have defined this iconic weapon. The result is not just a sword, but a masterpiece—a testament to the skill, artistry, and enduring legacy of the katana.
In the hands of a skilled warrior, a katana is more than just a weapon; it is an extension of the soul—a symbol of honor, courage, and indomitable spirit. And in the hands of a master swordsmith, it is a work of art—a masterpiece that transcends time and embodies the eternal quest for perfection.